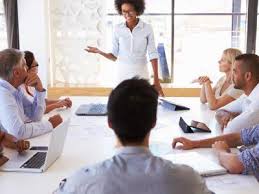
Pelatihan Improving Asset Performance with Total Productive Maintenance
Improving Asset Performance with Total Productive Maintenance
Pelatihan Improving Asset Performance with Total Productive Maintenance
Audience Profile
Asset Owners, Managers, Engineers, Designers, Planners, Trades Persons, Operators, Finance Managers, Safety Officers and all those who are eager to achieve sustainable improvement in Asset Operations Optimisation (formerly Total Productive Maintenance) and return on investment
Course Objectives
To equip those active in the management of productive and infrastructure assets with the
knowledge, skills and attitudes needed at the various stages in the life of an asset for optimising the quality and quantity of asset outputs, minimising risk and use of inputs, as required by the business plan.
The course will combine theoretical concepts and practical considerations to refine the understanding of:
* the urgency of introducing AOO in order to realise the full output potential of productive assets, avoid unnecessary investment in new assets and maximise revenue;
* the knowledge, understanding, skills and attitude necessary to perform AOO analyses
* to reduce losses and waste;
* the possibility to harness the full potential of the workforce that results in achieving
* remarkable asset performance improvements by introducing operator-maintainer principles;
* the development of a dynamic asset maintenance plan; and
* the power of the Overall Asset Effectiveness factor for single asset and processes for decision making.
What makes this course different?
The main difference is taking Total Productive Maintenance out of the maintenance realm and placing it where it belongs, with the operators. In any case former maintainers and operators will be transformed into process-based first-line asset management teams.
OUTLINE
Main Topics – Day 1
1. Total Productive Maintenance/Asset Operations Optimisation Explained
* Historic development of total productive maintenance
* Traditional manufacturing processes
* What are lean manufacturing and the Toyota Production System?
* How does the Toyota Production System link to Total Productive Maintenance?
* What are the effects of Just-In-Time manufacturing?
* What are the effects of reduced redundancy in utility networks?
* How do you maintain productive output?
* What is TPM and Asset Operations Optimisation?
* What are the objectives and goals of asset operations optimisation?
* How does Asset Operations Optimisation link to asset management?
* Definitions and acronyms
* What are the benefits of applying asset output optimisation?
* Why should you consider using asset operations optimisation?
* What is the asset operations optimisation process?
* How should you implement asset operations optimisation?
2. How to Identify Process or Assets, Functions and Performance Standards
* How to identify the process or assets for analysis?
* How important is an asset hierarchy?
* What are process and functional block diagrams?
* What is an asset register?
* Which asset register structure?
* How to collect data?
* Which asset to analyse first?
* Pareto analysis
* How to select significant functions?
* How do you assess risk?
* How can you rank asset reliability costs?
* How do you comprehensively describe functions?
* What are process or asset functions?
* Can you link functions to the current asset application?
* Can you include asset policy in function description?
* Can you link functions to the operator tasks?
3. What Are Losses, Waste, Causes, Effects, Detection, Consequences and Criticalities?
* What are causes for asset performance deterioration?
* what are causes for reduced asset Output?
* What are the six big losses?
* Asset down time (unplanned)
* Performance efficiency losses
* Process or output defects
* What are management-induced losses?
* Which losses happen in support functions?
* What are authority-induced losses?
* What is the difference between sporadic or chronic faults
* What is waste?
* How do you detect losses or waste?
* How do you link losses, waste and root causes?
* What are the effects of losses and waste?
* How to assess risk?
* What is the severity of fault consequences?
* What is the likelihood of occurrence?
* AS/NZS risk management
* How to calculate risk?
* Do you need to assess detectability?
* Syndicate exercise
4. What Is the Overall Asset Effectiveness Factor?
* What is Overall Asset Effectiveness?
* How to measure the Overall Asset Effectiveness?
* How to calculate Overall Asset Effectiveness
* What data do you need to collect?
* What is the Availability Factor or Operating Rate?
* What is the Performance Efficiency Factor?
* What is the Quality Efficiency Factor?
* What is the Planning Factor?
* Example of calculating the OAE
* Availability or Operating Rate
* Performance Efficiency
* Quality Efficiency
* Overall Asset Efficiency
* Second example of calculating the OAE
Main Topics – Day 2
* How to calculate the Overall Asset Effectiveness for Processes?
* How to perform a detailed production analysis?
* More definitions
* Information gathering
* What are the basic calculation inputs?
* How to perform the OAE calculation with Nakajima formulas?
* How to perform the OAE calculation with event time
* How to perform the OAE calculation based on good units
* Loss analysis and reconciliation
* How to interpret OAE/TAP calculations?
* What are the financial impacts of OAE Improvement?
* What is the impact on income?
* What is the impact on Return On Assets?
* What are Overall Asset Effectiveness goals?
* What are the benefits of improving the OAE?
* How do you raise the Overall Asset Effectiveness?
* Syndicate exercise
5. How to Eliminate Losses and Waste?
* How to achieve zero breakdowns?
* How to eliminate chronic faults?
* How to restore assets to optimal conditions?
* How to achieve zero faults?
* How to minimise set-up and adjustment losses?
* Single Minute Exchange of Dies (SMED)
* SMED example:
* Provide visual markings
* How to reduce idling and minor stoppage losses?
* How to reduce performance or speed losses?
* How to reduce chronic quality losses?
* How to reduce start-up or re-start losses?
* How to eliminate authority-induced losses?
* How to eliminate waste?
6. What Is the Asset Operations Optimisation Team Approach?
* How to develop optimum workplace conditions?
* Improve workplace environment
* Improve asset operability and maintainability
* The 5S housekeeping philosophy
* What is autonomous maintenance?
* Operator training
* Autonomous maintenance in support functions
* Extension of support function TPM to suppliers and distributors
* What is the maintainer program?
* Maintainer training
* Training of other personnel
* How to write standard task procedures?
* What is the team or small group approach?
* How to achieve an effective team?
* What are process-based teams?
* What are empowered employees?
* What are first-line asset managers?
* What are second-line asset Managers?
* who is the process team leader?
* Why share the benefits with the employees?
* What organisational structure should you adopt?
7. What Asset Operations Optimisation Analysis Sheets Can You Use?
* What do the Asset Operations Optimisation Analysis sheets look like?
* Function and performance level description
* Detection, causes and effects
* Risk assessment
* Task description and assessment of cost-effectiveness
* task frequency
* Syndicate exercise
8. How to Implement Asset Operations Optimisation?
* How to organise for AOO implementation?
* Do not hand the AOO analyses to consultants!
* What is the role of team members?
* What is the role of the facilitator?
* What are the steps of AOO implementation?
* Step 1 collect information regarding AOO
* Step 2 initial site audit and presentation to management
* Step 3 announce management’s decision to introduce aoo
* Step 4 form and train teams
* Step 5 establish vision, mission and aoo policies, strategies and goals
* Step 6 formulate a master plan for aoo development
* Step 7 perform a feasibility study.
* Step 8 start pilot implementations.
* Step 9 plant-wide aoo launch and improve asset effectiveness
* Step 10 establish an asset management program for operators
* Step 11 establish a program for the maintainers
* Step 12 provide operations and maintenance training
* Step 13 develop a designing for maintainability program
* Step 14 Implement AOO outcomes immediately
* step 15 perform one-off tasks
* step 16 continuous improvement
* Step 17 AOO progress audit
Main Topics – Day 3
* Work-based TPM/AOO analyses
METODE TRAINING
1. Presentation
2. Discuss
3. Case Study
4. Evaluation
5. Pre-Test & Post-Test
6. Games
Jadwal Training Update di Tahun 2023
Training Bulan Januari : 10-11 Januari 2023
Training Bulan Februari : 7-8 Februari 2023
Training Bulan Maret : 7-8 Maret 2023
Training Bulan April : 18-19 April 2023
Training Bulan Mei : 16-17 Mei 2023
Training Bulan Juni : 6-7 Juni 2023
Training Bulan Juli : 11-12 Juli 2023
Training Bulan Agustus : 22-23 Agustus 2023
Training Bulan September : 12-13 September 2023
Training Bulan Oktober : 10-11 Oktober 2023
Training Bulan November : 7-8 November 2023
Training Bulan Desember : 5-6 Desember 2023
Jadwal tersebut juga dapat disesuaikan dengan kebutuhan calon peserta
LOKASI PELATIHAN :
- Yogyakarta, Hotel Dafam Malioboro (7.250.000 IDR / participant)
- Jakarta, Hotel Amaris Tendean (7.750.000 IDR / participant)
- Bandung, Hotel Golden Flower (7.750.000 IDR / participant)
- Bali, Hotel Ibis Kuta (8.500.000 IDR / participant)
- Lombok, Hotel Jayakarta (8.750.000 IDR / participant)
INVESTASI TRAINING
Investasi Pelatihan tahun 2022 ini :
Investasi pelatihan selama dua hari tersebut menyesuaikan dengan jumlah peserta (on call). *Please feel free to contact us.
Apabila perusahaan membutuhkan paket in house training, anggaran investasi pelatihan dapat menyesuaikan dengan anggaran perusahaan.
Fasilitas Pelatihan di Diorama untuk Paket Group (Minimal 2 orang peserta dari perusahaan yang sama):
- FREE Airport pickup service (Gratis Antar jemput Hotel/Bandara)
- FREE Transportasi Peserta ke tempat pelatihan .
- Module / Handout
- FREE Flashdisk
- Sertifikat
- FREE Bag or bagpackers (Tas Training)
- Training Kit (Dokumentasi photo, Blocknote, ATK, etc)
- 2xCoffe Break & 1 Lunch, Dinner
- FREE Souvenir Exclusive
Jadwal Pelatihan masih dapat berubah, mohon untuk tidak booking transportasi dan akomodasi sebelum mendapat konfirmasi dari Marketing kami. Segala kerugian yang disebabkan oleh miskomunikasi jadwal tidak mendapatkan kompensasi apapun dari kami.
Technorati Tags: training production optimization of oil & gas pasti jalan,training optimalisasi produksi migas pasti jalan,training pengenalan production of oil & gas pasti jalan,training gas well loading prediction pasti jalan,pelatihan production optimization of oil & gas pasti jalan,pelatihan optimalisasi produksi migas pasti running